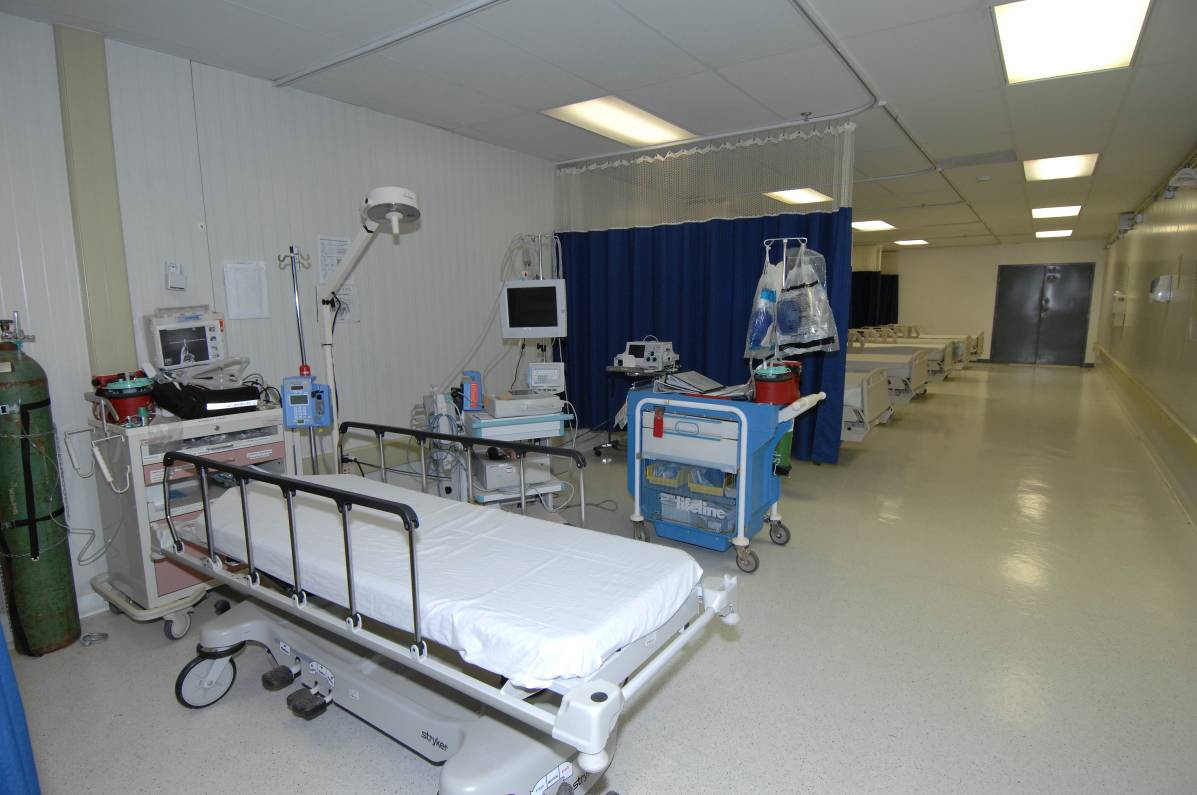
Photo by CC user DoD (public domain)
Several years ago it would be fair to say that hospitals were under scrutiny; there were all sorts of mysterious bugs being contracted and there were serious question marks regarding cleanliness and sterilization.
Now, the situation has turned on its head. Hospitals all around the country have implemented rigorous sterilization and disinfection plans that mean that their levels of cleanliness are beyond superb.
Most of the problems from several years ago focused on patient-care devices – the equipment that was constantly coming into contact with patients. Thanks to inventions such as the 3m attest, as well as some of the procedures highlighted below, hospitals are ticking all of the boxes in this department now. Here is how hospitals are cleaning up their act…
Cleaning occurs in a central processing department
This is perhaps one of the biggest changes in the overall process. Previously, cleaning may have been conducted anywhere – little thought might have been put into the location.
However, nowadays hospitals have a central processing unit which takes care of all cleaning of patient-care devices. It means that quality control is no longer an issue and the environment in which the equipment is being treated is also sterile – which may have been overlooked years ago.
The use of water before high-level cleaning products
Something else that has changed is the actual cleaning process. Now, hospitals insist that patient-care equipment is treated in multiple ways. Firstly, it should be cleaned with water and detergent, before then being passed forward for high-level disinfection.
The idea is that anything that is visible is removed immediately with the water, while the high-level cleaning agents take care of the deep cleaning that the naked eye might not be able to cope with.
Ensure that the chemicals are compatible with the device that is being treated
This is perhaps one of the more interesting points that hospitals are sticking to and previously, few would have envisaged a problem.
Due to the nature of some of the higher-level cleaning agents, some equipment is just not compatible. In other words, it is made out of materials that are hugely susceptible to these harsh chemicals and ultimately, it causes long-term damage.
As well as this, due to the way in which some metals respond to cleaning, hospitals are now being more careful than ever before on rinsing these chemicals away and not allowing them to dry and again cause long-term damage.
Check each device for any breakages
This final point is one of the most obvious, but it again may have been overlooked in the past.
Before the cleaning process even begins, a thorough inspection of all equipment should be conducted. It should be checked for any breakages or anything else that might hinder its use.
If any issues are found, the equipment should be discarded as a matter of urgency. If faulty equipment is being used to clean patient-care items, it goes without saying that there is a much higher risk of the objects not being completely sterile, which would then endanger patient health.